In-Depth Examination of Compliance Processes
"We must catch silent formatting errors before they compromise design history data, safeguarding our patients and our reputation." – QA Lead, Medtronic
This report delves into the document compliance processes specifically crafted for implantable device businesses. It emphasizes efficient methods to reduce human error when managing document revisions, ensuring that regulatory statements are prominently visible and the design history remains current. Recognized global brands have long championed clear, structured workflows, and the strategies included here mirror that commitment with actionable steps and detailed technical insight.
- IFU harmonization
- The process of ensuring interoperability and consistency in Instructions for Use across various device formats.
- Labeling matrix
- A structured approach to managing both primary and alternative document formats to ensure visible regulatory statements.
- Device family consistency
- An assurance strategy ensuring that all documents for a group of similar implantable devices meet the same stringent standards.
Document Preparation and Workflow Best Practices
Effective document preparation is the cornerstone of compliance. By standardizing naming conventions for both primary and alternate formats, companies can avoid the pitfalls of manual format errors. Utilizing document automation systems reduces the risk of oversight and promotes consistency in document outputs.
The adoption of version difference reports as a routine practice, common among innovative technology firms, contributes to maintaining the integrity of revised documents. Such systems highlight discrepancies, ensuring that each update aligns with established regulatory requirements.
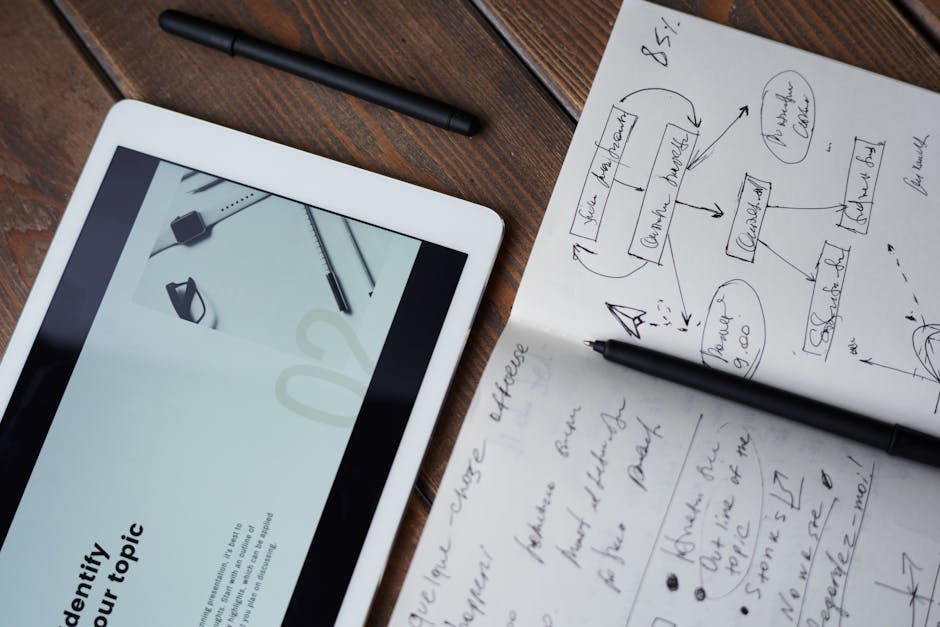
- Standardize naming conventions: A consistent label system for both primary and alternative formats.
- Utilize automation systems: Systems that bypass manual formatting errors by generating consistent outputs.
- Integrate version difference reports: Routine tracking of changes to ensure accuracy in revisions.
Common Errors and Their Resolutions
Several recurring document errors can significantly hamper compliance efforts. Notable issues include errors like alt_format_has_older_revision and approval_code_not_visible. Addressing these errors proactively is critical for maintaining both regulatory adherence and patient safety.
Practical remedies include synchronizing primary and alternate document versions through automated triggers during save events. Routine audits are also essential to detect anomalies such as minute isi fonts, temporary live preview copies, or inconsistencies between repeated excerpts and the primary text.
Software capabilities from providers like TVT and GlobalVision are instrumental in detecting these pitfalls early, thereby reinforcing a secure compliance framework.
Automation and Quality Control in Compliance
Leveraging automation significantly bolsters quality control by reducing manual review errors. Tools such as Tina5s aid in establishing an automated traceability system, centralizing file organization, and maintaining design consistency. This advanced level of automation not only streamlines the compliance process but also ensures that silent formatting errors do not go unnoticed.
A step-by-step integration of automation tools fosters an environment where real-time monitoring and robust workflow templates are the norms. This proactive system makes it possible to quickly identify and address discrepancies that could otherwise lead to regulatory lapses.
Click here for more automation details and case study insights
A brief industry case study demonstrated that automated version difference reports identified hidden discrepancies in design history files, a factor that could have led to severe non-compliance if left unchecked. Automation in this context not only enhances workflow efficiency but also fortifies compliance structures against unforeseen errors.
Such technological integration has proven especially effective in the implantable device sector, where even minor deviations can have significant repercussions.
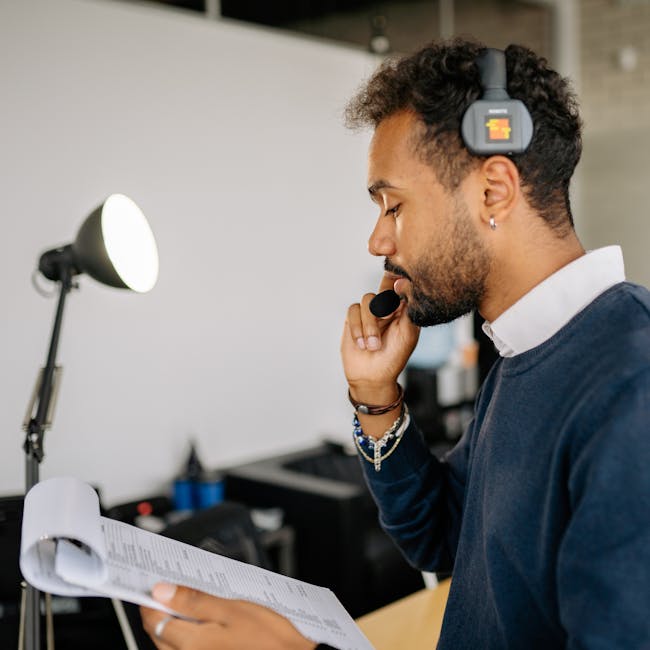
Pre- and Post-Streamlining: A Comparative Overview
A clear comparison between document sets before and after streamlining provides insight into the impact of efficient compliance practices. The table below outlines key differences in document formatting, ownership, and approval timelines.
Format | Owner | Approval Time |
---|---|---|
Legacy PDF | Manual Review Team | 7-10 days |
Automated HTML Output | Compliance Automation Team | 2-3 days |
Intermediate Draft Copies | Content Management | 5-7 days |
Finalized Digital Copies | Quality Assurance | 1-2 days |
Note: This table highlights efficiency gains from automated processes, improved ownership roles, and faster approval times. Keywords: document efficiency, compliance automation, quality control, regulatory adherence. |
Key Takeaways
A systematic approach to document compliance is essential—not only for regulatory adherence but also for protecting public health and upholding corporate reputation. By embracing technology-assisted strategies, companies can achieve uniform document quality and drastically reduce the risks of compliance errors.
Continuous monitoring and regular audits, paired with automated version difference reports, prove invaluable in maintaining a vigilant compliance posture. These practices ensure that all documents are consistently prepared and maintained in line with the evolving regulatory landscape within the implantable device industry.